Автоматизация ТОиР: изучаем эффекты, хитрости, подводные камни
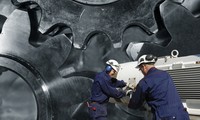
В периоды, когда рынок переживает сложную ситуацию, компании не останавливают ИТ-проекты, но сосредотачиваются на тех из них, которые имеют явный экономический эффект или повышают эффективность процессов. Ко второму типу относятся проекты внедрения информационных систем управления техническим обслуживанием и ремонтом оборудования на промышленных предприятиях. Зачем это нужно заводам, и к чему они должны быть готовы в ходе проекта?
Инициатива автоматизировать процессы техобслуживания и ремонта может исходить как от бизнес-руководства предприятия, так и от технических служб. Но кто бы ни был инициатором, менеджмент компании должен с самого начала проявить повышенное внимание к проекту и особенно к поставленным перед ним задачам, потому что зачастую цели у акционеров и у наемных работников разные, если не сказать – противоположные.
Для топ-менеджера главное – строгое соблюдение регламента работниками и прозрачность процессов. Он должен видеть, сколько оборудования вышло из строя, сколько в настоящий момент ремонтируется, сколько закуплено материалов, какая затоваренность складов и проч. И все это ему нужно в виде удобных аналитических отчетов. Эти же отчеты должны показывать, кто из работников наиболее эффективен, а от кого не добиться требуемого результата. На основе этой информации топ-менеджер может объективно оценить обстановку в подразделении и принять управленческое решение в отношении как персонала, так и рабочих процессов, бюджетов, объемов закупок и т.д.
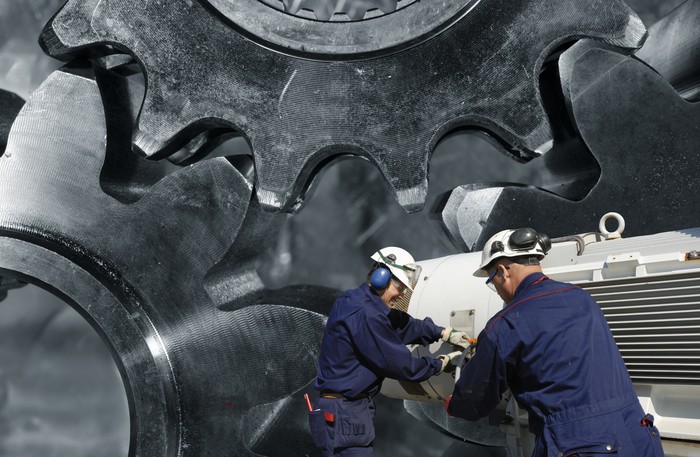
Есть и другая сторона. Руководители подразделений, которые по роду своих должностных обязанностей беспокоятся в первую очередь о нуждах своих служб, а не об эффективности предприятия в целом, стараются «перетянуть одеяло на себя». Например, такой важный на промышленном предприятии человек, как главный инженер, тоже заинтересован в автоматизации ТОиР, но для него это – способ не только улучшить управление, но и укрепить свои позиции в компании. На совещаниях с руководством он может оперировать регламентами, в которых указано, сколько человеко-часов нужно потратить на обслуживание одного станка, и доказать, что он не имеет достаточных людских ресурсов для выполнения планов, поэтому нужно либо увеличить штат, либо уменьшить план.
Технические подразделения тоже кровно заинтересованы в автоматизации ТОиР: им требуется формирование отчетов «по одной кнопке» для того, чтобы контролировать состояние дел самим и быстро отвечать на запросы информации со стороны руководства. Но при условии, чтобы они в любой момент могли эту информацию подкорректировать.
Компромисс
Автоматизация ТОиР – это, по большому счету, типичный ИТ-проект, поскольку он предусматривает внедрение информационной системы и наполнение ее данными. Это может быть модуль ERP или отдельное решение – каждый выбирает то, что ему выгодно и чем будет удобнее пользоваться.
При обсуждении проектов можно наблюдать еще одно различие в подходе бизнес-менеджеров и руководителей технических служб. Первые хотят получить прогрессивное решение и просят включить различные опции, вплоть до трехмерных моделей всех деталей. Вторые видят в этом чрезмерное усложнение своей работы. Ведь они и так знают, как выглядят детали, а человека в штат для поддержки каталога моделей им никто не даст. Кроме того, создание тысяч и тысяч 3D-моделей «съест» проектный бюджет и отложит его старт на неопределенный срок.
В этих вопросах всегда нужно искать разумный компромисс. Подход «я хочу видеть в системе каждую втулку» не годится, потому что он нереалистичен и экономически невыгоден предприятию. Но и противоположный подход «не надо этих рисунков и описаний, я и так все знаю» вреден, потому что не поддерживает преемственности. Наверное, в каждой службе с долгой историей существования могут рассказать о сотрудниках, которые «знали все», но потом уволились и унесли с собой знания, которые должны принадлежать всему предприятию. Да, у них были ученики, но традиционный способ обучения заключался в том, что опытный рабочий брал с собой новичка, показывал, где и какие действия нужно произвести, и давал ему толстый мануал по ремонту этого оборудования. В результате знания, что именно нужно делать, и какой смысл был в показанных мастером действиях, ученик получал самостоятельно, и тратил на это много времени.
Выбор
Правильно внедренная информационная система обладает полным комплектом знаний обо всех процессах обслуживания и ремонта. На основе стандартной технологической карты можно составлять чек-листы с описанием необходимых видов работ, а по ним, например, служба главного инженера может контролировать нормативные сроки выполнения работ. Кроме того, она позволяет планировать деятельность обслуживающего персонала, поскольку сроки ремонтов и обслуживания известны заранее. В этом заключается одно из важнейших ее преимуществ перед «хаосом».
Хорошо, если на заводе уже есть автоматизированная система с данными по оборудованию. Например, в 1990-е были популярны самописные приложения для расчета производственных мощностей. И эти данные можно перенести в промышленную систему управления ТОиР. Но и здесь возникает проблема: экспертизы по самописным системам больше нет, потому что разработчики давно ушли. Данные в них еще вводятся, но как все работает, уже никто не знает. Документировать разработки в те годы было не принято.
В последние 10-15 лет многие компании внедрили современные промышленные финансовые системы, ERP – с ними интегрироваться легче, если готова нормативно-справочная информация, потому что у бухгалтеров и у инженеров одно и то же оборудование может быть записано по-разному.
«Каждая компания встает перед вопросом, какую информационную систему управления ТОиР внедрять. Нужно исходить из специфики своей ситуации – например, уже может быть внедрена ERP, к которой существует модуль управления ТОиР, или же такой системы нет, а есть условия для внедрения полноценного EAM-решения (Enterprise Asset Management – управления активами предприятия), – поясняет Дмитрий Какаев, начальник отдела управления производственными активами RedSys. – Мы традиционно работаем с платформой IBM Maximo Asset Management. Это очень мощное, качественное и известное решение, с большой историей проектов, среди которых есть и российские в РЖД, «Роснефти» и других крупных организациях».
Начинаем с документации
На старте проекта все должны быть готовы к тому, что интегратор, зайдя на предприятие, найдет там хаос. Его классический вариант – таблицы Excel по шаблонам, которые каждый сотрудник настраивал под себя сам. Мало того, что отсутствует единая база данных по предприятию, нет преемственности (не каждый увольняющийся сотрудник будет объяснять преемникам нюансы своих шаблонов) – такие таблицы еще и неэффективны и не объективны. Каждый раз при планировании мероприятий ТОиР на следующий период сотрудник только меняет в таблице дату и вписывает новые цифры напротив видов работ. При этом нельзя проконтролировать, учтены ли реальные трудозатраты на тот или иной тип оборудования в этом году, данные о том, какое оборудование ломается чаще, какие объемы материалов уже находятся на складе. Например, можно год за годом закупать по 10 тонн масла, но без данных о складских остатках нельзя скорректировать эти закупки. На этом фоне все требуют единое хранилище данных и автоматизацию учета и отчетности.
На этом пути компанию чаще всего ждет необходимость разработки единой базы нормативно-справочной информации. Это долгий, трудоемкий и дорогостоящий процесс, который включает паспортизацию оборудования, складов, создание технологических карт обслуживания, ведение спецификаций квалификации сотрудников. Но без него невозможно построение системы ТОиР, поскольку НСИ – это ее база. Изменится классификатор – придется вносить изменения в систему.
Насколько глубокая детализация требуется при заведении оборудования в систему, ведь оно – не цельный кусок металла, а сложное устройство, состоящее из множества комплектующих с разными сроками эксплуатации, износом и т.д.? Мы уже показали, что записывать отдельно каждую втулку не нужно, потому что такой проект не закончится никогда. Заносят обычно то, что имеет собственный инвентарный номер. А если разные части одного устройства (например, станка с ЧПУ) требуют обслуживания специалистами разного профиля и разных служб, тогда можно и разделить на электронную и электромеханическую составляющие.
Внимание бизнес-процессам
Следующий этап – описание бизнес-процессов предприятия. Если они уже оптимальны, можно внедряемую систему подстроить под существующее положение дел. В этом случае пользователи получают только инструкцию по пользованию системой. Но часто приходится менять процессы согласования, чтобы сократить количество итераций и копий документов. Предприятие должно быть готово к изменению процессов, а сотрудники – к тому, что теперь они будут работать в информационной системе.
Можно привести такой пример неэффективной организации процессов при отсутствии единой системы управления ТОиР. Механик обходит производство по заданному маршруту, проверяет работу оборудования. Ему сообщают, что такой-то станок сломался. Он идет за ремкомплектом, возвращается, приступает к ремонту и обнаруживает, что для этого требуется второй человек – электрик. В это время заканчивается смена. Механик вешает табличку «Не работает», пишет заявку на электрика на завтра и идет домой. На следующий день встречается с электриком, объясняет ему задачу, оба начинают ремонт – итого два дня потеряны.
Как утверждают специалисты RedSys, при наличии информационной системы по записям механика можно сразу увидеть, какое оборудование сломано, какое последнее рабочее задание было, какие материалы нужно сразу забрать на складе. Электрика можно отправить сразу же, а не на следующий день, когда на месте будет тот самый механик, который знает, в чем проблема со станком.
Планирование ремонтов
После подготовки нормативно-справочной информации, описания бизнес-процессов и непосредственно внедрения ЕАМ-системы начинается этап планирования деятельности: что и как нужно обслуживать и ремонтировать. Существуют два подхода. Первый – ремонт по факту. Это «экономный вариант», когда производится не профилактический ремонт через определенные промежутки времени, а по заявке, когда что-то сломалось. На таких предприятиях в план закладываются прогнозные данные, что может потребовать ремонта. Чаще всего это не очень большие заводы, которым не нужна и ЕАМ-система, а поломка оборудования влечет небольшой ущерб.
Второй подход распространен на предприятиях с тысячами единиц оборудования и десятками тысяч работников, где любой сбой означает серьезный ущерб. Это – планирование по регламенту. Каждый станок нужно обслуживать с определенной периодичностью, следовательно, можно рассчитать, сколько потребуется материалов, какие людские ресурсы и какие могут потребоваться услуги сторонних организаций. Важность последнего пункта не стоит недооценивать, потому что замена сломавшейся детали с заказом у зарубежного производителя может занимать несколько месяцев, а совокупная стоимость доходить до десятков и сотен тысяч долларов. В реальных ситуациях, когда возникали такие проблемы, расчеты показывали, что лучше каждые несколько месяцев останавливать станок на два-три дня, делать профилактику и контролировать состояние всех узлов, чем допускать длительный простой оборудования.
В результате, когда данные о планируемых ремонтах заведены в систему, руководство предприятия получает точные данные, какие материалы необходимо закупить, какие есть на складе и как надолго их хватит. А начальники подразделений имеют на руках расчеты трудозатрат и могут мотивированно обсуждать со своим руководством планы и ресурсы для их выполнения.
Выгоды
Суммируя вышесказанное, можно описать преимущества, которые дает автоматизация ТОиР. Во-первых, лица, принимающие решения, получают инструмент мониторинга и контроля ситуации на производстве в разрезе состояния оборудования. Знать, сколько оборудования сломано – важный показатель не только для предприятия в целом, но и для обслуживающего подразделения – их KPI зависят от количества простоев.
Если задаться вопросом, какие конкретно суммы можно сэкономить – на него ответить сложнее. Информационные системы ТОиР непосредственно не участвуют процессе производства товаров и услуг. Но в рамках подхода «Сэкономил – значит заработал», являются эффективным инструментом для производственного и руководящего персонала. Оперативное предоставление актуальной информации для принятия управленческих решений позволяет уменьшить затраты на аварийные и сверхурочные работы, сформировать необходимый и достаточный аварийный запас МТ, а самое главное сделать прозрачным процесс формирования бюджета обслуживающих подразделений предприятия.
Пожалуй, прямое влияние на бюджеты дают снижение затоваривания складов лишними материалами и сокращение простоев оборудования.
В том числе компания экономит деньги то за счет более эффективной организации труда. Сюда относится и оптимизация плана обслуживания. В частности, план ремонтов может быть интегрирован с производственным планом, и на профилактику оборудование будет вставать только когда оно не задействовано или не выполняет срочный заказ.
Кроме того, автоматизация позволяет контролировать выполнение ремонтов своими сотрудниками и подрядчиками. И, если что-то сделано не так, как надо, можно принять меры внутри коллектива или предъявить претензии подрядчикам.